Overview:
Work Order definition: The plan to create a mix or set of mixes.
Alternate Terms for Work Order: Prescriptions, Recepies, Jobs.
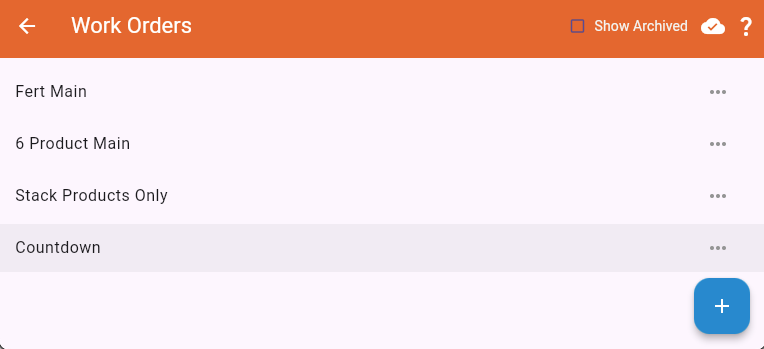
Plus button in bottom right corner to create a new work order.
Overview list of Active/Archived work orders. Archived work orders will only show on
app.mixmate.com
The menu button

at the right of each work order shows the following modal:
- Archive - archives the work order and if the work order is archived for over 12 months straight, it gets removed from the system
- Mark as Complete - Marks the work order complete and archives it.
- Copy - creates a copy of the work order to use a starting
Creating / Editing work orders:
Work Order filters:
Only for Mixmate: Limits this work order so ONLY the selected Mixmate can run it. Only shows if you have more than 1 Mixmate.
Only for User: Limits this work order so ONLY the selected User can run it. Only shows if you have more than 1 User.
Use As:
Work Order: Use this when you have a total target that you want to count down to and complete when that target is reached.
Reusable Mix: Use this when you have a mix that you aren't sure how many times you will need to use it.
Use Totals: Use this when you want to create a ratio mix or when you know the total amount of each product you want in the Mix
Use Rates: MOST COMMON - you know the application rate of each product and want adjustability at the time of mixing
Filling out a work order when Use As is set to Work Order and Use Rates:
Work Order Number: REQUIRED - This is an alpha numeric value usually defined by the work order number generated by another system, or can be things such as Grower/Farm/Field etc. This line is what shows in the dropdown on the Mix tab.
Final State of Mix: REQUIRED - Liquid or Dry - This sets whether the result of the Mix is a liquid or a dry.
Destination: This is container where the mix is going.
Carrier: This is typically the largest volume product in the Mix where all other products get added to this product. Most common carrier product is Water.
Overall Work Order Size: REQUIRED - This size and unit of measure defines the total area or volume that the work order represents. It may take multiple mixes to complete a work order.
Application Rate Value/Rate: required with carrier selection - Defines the final application rate of the mix. MUST be greater than all of the rates of the products added together.
Set Planned Mix Size: REQUIRED This is setting the initial Mix size when selecting this work order on the Mix tab. These are the following options to define the Planned Mix Size.
- Destination Capacity - Sets the Mix Size to match the size of the selected destination above
- Number of Splits - Divides the work order total by the number of splits defined with this selection
- User Defined - Sets the mix size to the value set by the user when this option is selected
- Work Order Size - complete the entire work order with 1 mix
Adding Products to this work order:
Products: This is the list of products and preferred Mix order is Top to Bottom
Edit Mix Order: Gives the ability to rearrange the order of the products in the list
Add Product Amount: Opens the editing page to add a product and define the application rate of that product
Product: REQUIRED - The selected product for this spot in the main list and the user can add a new product if they don't already have the product in the system. More information can be found under Products.
Click Here
Product Rate: REQUIRED - This is the value of the intended application rate of the product
Rate: REQUIRED - This is the associated units to the value of the intended application rate of the product.
Rinse Amount/Rinse Unit of Measure: The value entered here overrides the default rinse amount set on the product when used in this work order.
Filling out a work order when Use As is set to Reusable Mix and Use Rates:
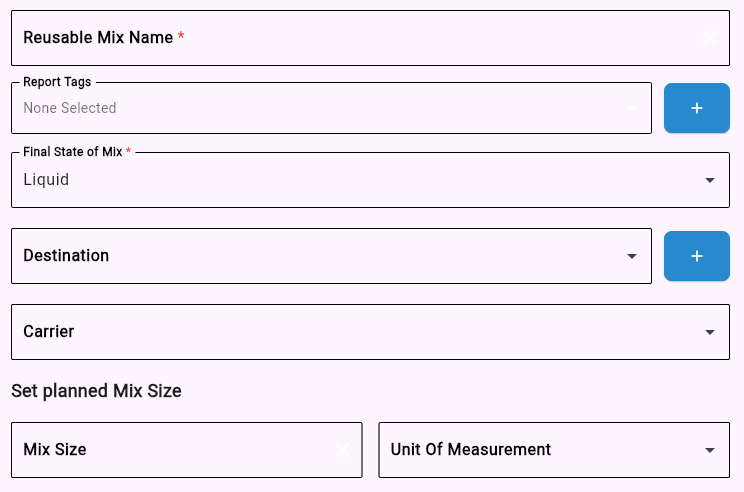
Reusable Mix Name: REQUIRED - This is an alpha numeric value. This line is what shows in the dropdown on the Mix tab.
Report Tags: Pre defined search tags that get applied to work records used for filters. Report Tags can also be added when saving each mix - More information found in
Report Tags
Final State of Mix: REQUIRED - Liquid or Dry - This sets whether the result of the Mix is a liquid or a dry.
Destination: This is container where the mix is going.
Carrier: This is typically the largest volume product in the Mix where all other products get added to this product. Most common carrier product is Water.
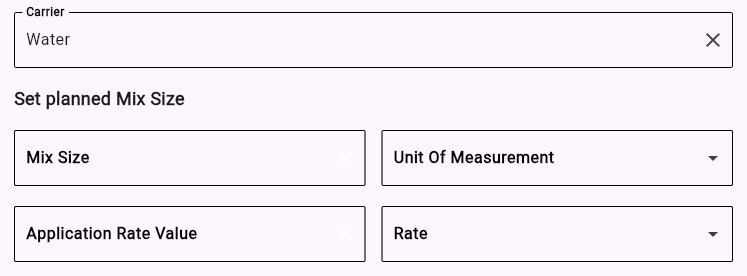
Planned Mix Size: REQUIRED - This size and unit of measure defines the initial size of the mix when this is selected in the Mix tab.
Application Rate Value/Rate: required with carrier selection - Defines the final application rate of the mix. MUST be greater than all of the rates of the products added together.
Adding Products to this reusable mix:
Products: This is the list of products and preferred Mix order is Top to Bottom
Edit Mix Order: Gives the ability to rearrange the order of the products in the list
Add Product Amount: Opens the editing page to add a product and define the application rate of that product
Product: REQUIRED - The selected product for this spot in the main list and the user can add a new product if they don't already have the product in the system. More information can be found under Products.
Click Here
Product Rate: REQUIRED - This is the value of the intended application rate of the product
Rate: REQUIRED - This is the associated units to the value of the intended application rate of the product.
Rinse Amount/Rinse Unit of Measure: The value entered here overrides the default rinse amount set on the product when used in this work order.
Filling out a work order when Use As is set to Work Order and Use Totals:
This is probably the least common configuration because the mix size is set to the totals of the products added together, but could take multiple mixes to complete.
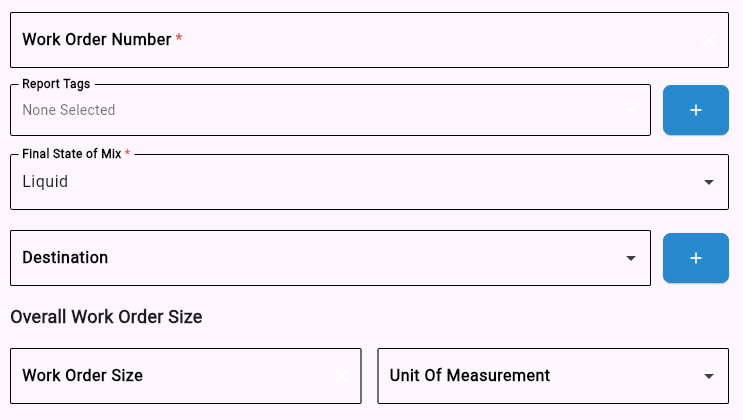
Work Order Number: REQUIRED - This is an alpha numeric value usually defined by the work order number generated by another system, or can be things such as Grower/Farm/Field etc. This line is what shows in the dropdown on the Mix tab.
Report Tags: Pre defined search tags that get applied to work records used for filters - More information found in
Report Tags
Final State of Mix: REQUIRED - Liquid or Dry - This sets whether the result of the Mix is a liquid or a dry.
Destination: This is container where the mix is going.
Overall Work Order Size: REQUIRED - This size and unit of measure defines the total area or volume that the work order represents. It may take multiple mixes to complete a work order.
Adding Products to this work order:
Products: This is the list of products and preferred Mix order is Top to Bottom
Edit Mix Order: Gives the ability to rearrange the order of the products in the list
Add Product Amount: Opens the editing page to add a product and define the total amount of that product for each mix.
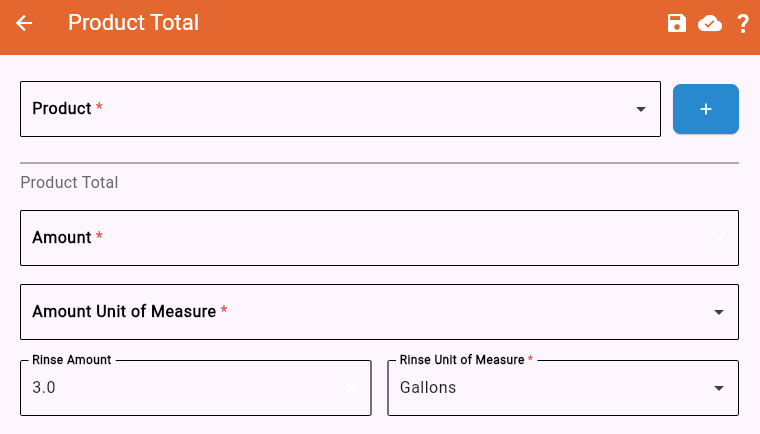
Product: REQUIRED - The selected product for this spot in the main list and the user can add a new product if they don't already have the product in the system. More information can be found under Products.
Click Here
Amount: REQUIRED - This is the value of the intended amount of product to be added to the mix
Amount Unit of Measure: REQUIRED - This is the associated units to the value of the intended amount of product to be added to the mix
Rinse Amount/Rinse Unit of Measure: The value entered here overrides the default rinse amount set on the product when used in this work order.
Filling out a work order when Use As is set to Reusable Mix and Use Totals:
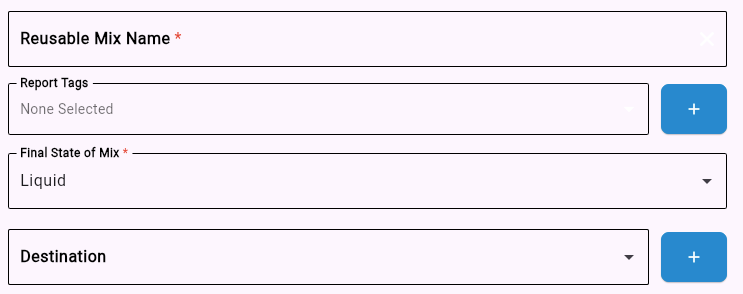
Reusable Mix Name: REQUIRED - This is an alpha numeric value. This line is what shows in the dropdown on the Mix tab.
Report Tags: Pre defined search tags that get applied to work records used for filters. Report Tags can also be added when saving each mix - More information found in
Report Tags
Final State of Mix: REQUIRED - Liquid or Dry - This sets whether the result of the Mix is a liquid or a dry.
Destination: This is container where the mix is going.
Adding Products to this reusable mix:
Products: This is the list of products and preferred Mix order is Top to Bottom
Edit Mix Order: Gives the ability to rearrange the order of the products in the list
Add Product Amount: Opens the editing page to add a product and define the total amount of that product for each mix.
Product: REQUIRED - The selected product for this spot in the main list and the user can add a new product if they don't already have the product in the system. More information can be found under Products.
Click Here
Amount: REQUIRED - This is the value of the intended amount of product to be added to the mix
Amount Unit of Measure: REQUIRED - This is the associated units to the value of the intended amount of product to be added to the mix
Rinse Amount/Rinse Unit of Measure: The value entered here overrides the default rinse amount set on the product when used in this mix.